
9 trends driving electrification in automotive design
André Voshart
Electronics AutomotiveAutomotive design is undergoing a seismic shift as electrification reshapes the industry. Today’s vehicles are no longer just mechanical marvels—they are becoming mobile power hubs brimming with advanced electronics.
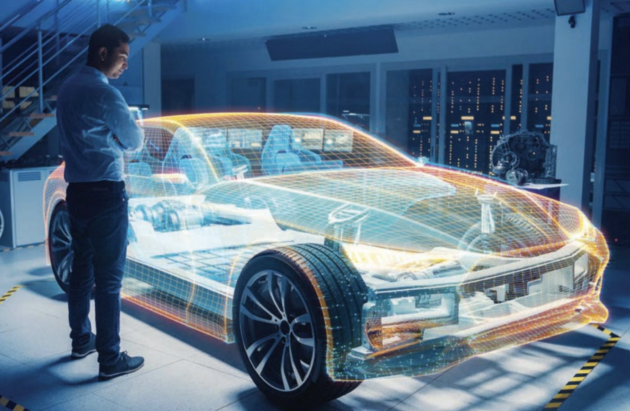
Increasing electrification presents an opportunity to rethink how vehicles are designed.
Electrification is not just about swapping internal combustion engines for electric motors; it’s a comprehensive overhaul of a vehicle’s energy ecosystem. With the growth of electric vehicles (EVs) and the emergence of 48-volt systems, engineers are tasked with integrating complex electrical architectures that improve efficiency, enhance performance and support an ever-expanding array of features.
This transition presents an opportunity to rethink how vehicles are designed. Design Engineering interviewed several industry leaders about the nine technologies trends driving this evolution and the strategies engineers are adopting to overcome challenges.
1. Shift to electrification
The electrification of automobiles is transforming vehicle design, offering engineers unprecedented flexibility and opening the door to new innovations. “Without the need to accommodate a traditional internal combustion engine, auto manufacturers have more flexibility in where to distribute batteries and charging ports,” says Shawn Luke, technical marketing engineer at DigiKey. This shift has enabled manufacturers to prioritize passenger and cargo space, enhancing both comfort and utility.
As the market evolves, the variety of available EVs continues to expand. But challenges remain, including high costs and a lack of standardization across the industry. These hurdles are likely temporary as technology advances and production scales up. Luke is optimistic: “The cost of the vehicles will likely decrease as technology advances and production ramps up.”
The ongoing shift toward electrification also signals a growing consumer demand for advanced safety and comfort features, as well as environmentally friendly transportation options. Meeting these demands requires a robust supply of suitable components.
2. Switch to 48-volt architecture
The shift from 12- to 48-volt electrical systems is revolutionizing automotive design. “By quadrupling system voltage, 48-volt technology boosts electric turbocharging, regenerative braking, infotainment systems and battery preconditioning for auxiliary charging,” says Frank Homann, vice-president and general manager of Connected Mobility Solutions at Molex. These advancements bring EVs closer to matching the range and convenience of internal combustion engine vehicles.
In addition to boosting performance, 48-volt technology is pivotal for increasing power efficiencies across advanced systems like sensors, actuators and control units. “The delivery of higher current and voltage also is crucial to increasing power efficiencies in sensors, actuators and control units needed for advanced driver assistance systems,” he explains. But this shift brings new challenges, including increased electromagnetic interference and added complexity to wiring and harness designs.
To address these challenges, design engineers must prioritize connector performance and reliability. Homann suggests modular platforms as a solution: “Designers should seek modular platforms consisting of interchangeable components, including electric motors, inverters, along with DC-DC converters and batteries.” Such platforms allow for greater flexibility and scalability, making it easier to integrate 48-volt systems into new vehicle designs.
From DigiKey’s perspective, the 48-volt bus architecture also simplifies complex power wiring harnesses, offering significant benefits for manufacturers and consumers alike. “At higher voltages, the complex power wiring harness can be simplified, further reducing weight and cost,” Luke says. This reduction not only streamlines production but also enhances the overall efficiency of EVs.
While some vehicles have already adopted 48-volt systems, many others remain to be redesigned to fully leverage their advantages.
Luke underscores the competitive edge this transition offers: “Any change that gets people on the road sooner and at a cheaper price compared to the competition is welcomed by drivers and manufacturers.”
Gregory Green, director of automotive customer programs at Vicor Corp., highlights the impact this shift will have to the sector. “The transformation from all the 12-volt loads to 48-volt loads is probably going to take 10 to 15 years,” he says. “It’s a very big trend within the industry because automakers want to reduce the weight and cost, and the 48-volt transition is a big improvement in cost and weight.”
3. Drive toward autonomy
As the automotive industry accelerates toward higher levels of autonomy, the demand for advanced driver-assistance systems (ADAS) is reshaping vehicle design.
“The main challenge is scaling the necessary compute power in a cost-effective manner,” says Cyril Clocher, senior director at Renesas. To meet this demand, Renesas has adopted a chiplet approach—a modular design strategy that enables scalable performance without additional overheads. “The chiplet approach extends the base SoC with an AI accelerator through standardized interconnects.”
This architecture not only allows for enhanced performance scalability but also offers flexibility for seamless upgrades, enabling vehicles to accommodate evolving AI models. This adaptability is critical as automakers race to implement ADAS features that enhance safety, such as collision avoidance and lane-keeping assistance, while preparing for future levels of autonomy.
Pierre Olivier, CTO at LeddarTech, emphasizes the growing importance of data in advancing ADAS and autonomous driving (AD). “Recent trends in AI show that data is increasingly becoming both the bottleneck to better AD performance and the key to reaching the level of performance required for safe and reliable ADAS and AD,” he says. The challenge lies in obtaining high-quality data for training and validating AI models—a task that traditional methods struggle to fulfill efficiently.
To address this, innovative simulation technologies are emerging as a game changer. These methods reduce the reliance on live data collection and annotation, streamlining the development process for ADAS systems.
4. Wireless charging
The evolution of wireless charging in the automotive industry is accelerating with the adoption of Qi 2.0 and upcoming Qi v2.x standards. “With the arrival of Qi2.0, automotive OEMs and Tier 1 suppliers are giving automotive wireless charging solutions a major boost,” Molex’s Homann says. According to ResearchAndMarkets, the installation rate of wireless charging modules in new cars jumped from 6.9 per cent in 2020 to 44.1 per cent by mid-2024, reflecting the technology’s growing appeal.
Qi 2.0 has been pivotal in restoring consumer trust in wireless charging, thanks to its 15W unified charging standard and the introduction of the magnetic power profile. “Qi 2.0 meets consumer demand for medium- and higher-power wireless charging,” he explains. Looking ahead, iterative releases in 2025 and 2026 will enable 25W and 50W wireless charging, marking a significant leap forward from the early 5W solutions.
Staying current with these advancements is essential to meet growing demand for higher-power wireless charging. While private protocols capable of reaching 40W to 50W exist, Homann notes that “alignment with WPC initiatives and standardized solutions offers a more seamless path to unified wireless charging.”
5. Software-defined vehicles
The automotive industry is undergoing a significant transformation from hardware-centric designs to software-defined vehicles (SDVs). This shift enables enhanced user experiences, personalization and seamless connectivity.
This evolution is fundamentally driven by factors like the facilitation of secure over-the-air (OTA) updates, modular and collaborative hardware and software, increasing silicon consolidation and integration, and the reduction of wiring harness complexity.
At the heart of SDVs is the decoupling of hardware and software, allowing for OTA updates like those in smartphones but with added layers of safety and security. Renesas’ RoX SDV platform exemplifies this approach by combining cloud-native development with a customizable simulation environment, facilitating both pre- and post-development deployment.
As vehicles incorporate more software, traditional distributed electrical/electronic (E/E) architectures struggle to meet demands for computing capacity, reliability and OTA upgradeability. LeddarTech’s Olivier notes that “the promises of hardware-centric reliability and maintainability are no longer met, and manufacturers are struggling to deliver quality software-based features.” To address these challenges, solutions from enterprise computing—such as virtualization, containerization and standardization—are being adopted, necessitating a move toward centralized or zonal architectures.

The automotive industry is increasingly shifting from central to zonal architectures, which simplifies vehicle design by consolidating electronic control units into specific zones. (Credit: Vicor)
6. Zonal architecture
The automotive industry is increasingly adopting zonal architectures to support the evolution of SDVs. This approach simplifies vehicle design by consolidating electronic control units (ECUs) into specific zones, reducing wiring complexity and enhancing scalability. By organizing the vehicle’s E/E systems into zones, manufacturers can more easily implement updates and integrate new technologies.
As vehicles transition to zonal architectures, the demand for compact, durable connectors has surged. Molex’s Homann highlights that these connectors “blend the best of miniaturization and ruggedization,” enabling critical applications such as zone-to-zone communications, infotainment systems and high-resolution displays.
The shift to zonal architecture also helps reduce copper use and wiring complexity. “When you go to 48 volts, that power wiring goes from six millimeters to two and a half millimeters,” Vicor’s Green says. “The copper content goes down by about two-thirds, so in a 48-volt zonal application, you start by sending 48 volts around the car. That reduces your wire harness size and takes up to 85 per cent of the wire harness weight out.”
The convergence of interconnect ruggedization and miniaturization is facilitating major innovations.
7. High power density
Vicor’s focus on power density has revolutionized power systems in automotive applications. The company says its compact DC-DC converters, offering up to 10,000 watts per cubic inch, allow manufacturers to reduce vehicle weight by up to 25 kilograms and cut costs by $100 per vehicle.
“We are very comfortable saying we have the highest power density on the planet,” Green says. “Within an EV, there are several power conversions, particularly between the 800-volt main battery and the 48-volt and 12-volt systems.”
He says this innovation supports miniaturization and integration. “Reducing the size and weight of DC-DC converters allows OEMs to integrate things such as onboard charging systems, creating a pathway to downsized, efficient designs.”
8. Centralized compute architecture
The shift from distributed to centralized compute architecture is transforming vehicle design. “The E/E architecture is moving toward a centralized compute model, reducing the number of ECUs and wiring harnesses,” Renesas’ Clocher says. By integrating multiple domains into a single module, manufacturers can streamline design while enhancing performance and reliability.
One of the challenges in this transition is ensuring robust isolation between safety-critical and non-critical functions. “The recently launched R-Car Gen 5 uses the latest technology node for industry-leading power efficiency and incorporates unique hardware-based freedom from interference (FFI) technology for stringent isolation,” he says. This technology securely separates critical systems like brake-by-wire, assigning them redundant domains with independent CPU cores, memory and interfaces. This architecture prevents failures in non-critical domains from affecting essential safety functions.
Many automakers are also looking toward hybrid architectures—where zonal controllers handle local processing while a centralized compute unit makes high-level decisions.
9. Consolidation and collaboration
The automotive industry is undergoing a significant transformation in how it approaches innovation, marked by a shift toward consolidation and collaboration. “Over the last decades, we have seen the auto industry move from vertical integration to outsourcing,” LeddarTech’s Olivier says. Now, as software-based features become the primary differentiator in vehicles, OEMs and Tier 1 suppliers are grappling with the challenge of meeting consumer demands for the technologies like autonomous driving.
Consolidation among industry giants, such as Stellantis, Marelli and ZF, is emerging as a critical solution to streamline resources and strengthen capabilities. But Olivier emphasizes that collaboration, where historical competitors share platforms and technology innovations, will become “more and more prevalent.” This approach enables companies to pool expertise and resources—accelerating the pace of innovation.
Print this page
Advertisement
<