
PAMI brings new life to machinery with custom parts, modern controls
André Voshart
ElectronicsSaskatchewan’s PAMI specializes in helping clients maintain the viability of legacy equipment by designing and building replacement parts such as transmission controllers and wiring harnesses.
At PAMI—the Prairie Agricultural Machinery Institute—legacy equipment gets a second chance at life.
Equipped with cutting-edge tools for electro-hydraulic control integration, custom harness prototypes and assembly testing, PAMI serves both new machinery and retrofit projects.
Many fleet operators and customers come to PAMI looking for solutions for obsolete equipment. They need help developing new setups that integrate modern automation and control systems, allowing the equipment to function more efficiently than originally designed.
“How do you come up with a new a new setup that allows us maybe some further level of automation control beyond something that was originally designed?” asks Bryan Lung, PAMI’s director operations. He says their small but mighty team specializes in retrofitting these machines, providing updated, reliable solutions that extend their lifespan and enhance their operational capabilities while addressing the lack of available original components.

When designing wire harnesses, PAMI emphasizes the importance of breaking them into smaller, manageable sections for ease of assembly and serviceability. (Credit: PAMI)
Harnessing new life
Humboldt, Sask.-based PAMI’s Electronics Lab and Cable Shop offers a full suite of capabilities for designing, assembling and testing advanced electrical and electronic systems. Specializing in schematic and harness design, the lab plays a crucial role in developing control system components for various industries.
When a customer encounters an issue, the PAMI team starts by reviewing existing schematics and documentation of the product. “We’ll round up whatever information we can find on the existing product,” technical team lead Derek Schultz says. “So existing schematics, drawings, things like that.”
Then from there, using CAD modelling and other tools, they design a new solution that often improves upon the original functionality, sometimes adding automation or control upgrades.
The cable shop uses advanced computer-aided manufacturing to ensure precision and efficiency in building wire harnesses. Engineers design these machines using SolidWorks and Creo, generating 3D harness routing for accurate assembly.
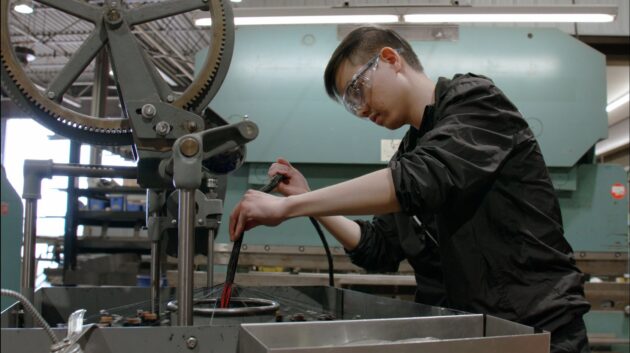
Harnesses are braided with temperature- and abrasion-resistant yarn for durability, then tested before being installed. (Credit: PAMI)
When designing wire harnesses, they emphasize the importance of breaking them into smaller, manageable sections for ease of assembly and serviceability. Using Zuken’s Harness Builder for E3.series software, the team generates accurate form board layouts, bills of materials and wire cut lists, which are then fed into a Schleuniger cutter that measures, cuts and labels wires to precise specifications. Once the wires are prepared, they are laid out, assembled and undergo rigorous testing through an MPT tester, which checks for electrical continuity, insulation strength and proper function.
This modular approach reduces costs and complexity while ensuring that parts are easier to replace, especially in rugged industries like agriculture and mining.
Following testing, the harnesses are braided for added durability using temperature- and abrasion-resistant yarn. This braiding is performed using two specialized machines—a 36-carrier machine for larger cables and a 16-carrier for smaller ones. Once the components are braided for durability, they undergo a final round of testing before being added to inventory or installed in machines.
Once validated, the parts can be manufactured in small or large production runs. This process ensures that clients can extend the life of their machinery without needing to replace entire fleets, providing a cost-effective solution while ensuring that updated equipment performs reliably.
According to Schultz, this streamlined approach drastically reduces troubleshooting time, making the machinery operational within hours instead of weeks. This streamlined process allows them to produce fully functional harnesses efficiently, transforming a complex production task into a well-structured, quality-controlled operation.

PAMI was tasked with developing a solution that would extend the life of Big Bud tractors while ensuring operational reliability. (Credit: PAMI)
Big Bud
The Big Bud tractor project revolved around reviving outdated machinery by designing a new transmission controller, as the original replacement parts were no longer available. And what’s more, the owners of Big Bud tractors have a strong attachment to these machines.
“The people that have Big Bud tractors are kind of like people that have Harley’s—they love their machines,” Lung explains. “They’ll put all kinds of love labour into keeping their tractors rolling. It’s a piece of history, and in their minds, it’s the ultimate machine. So there’s definitely a desire that goes beyond just patching it to make it work.”
PAMI was tasked with developing a solution that would extend the life of these tractors while ensuring operational reliability. The team had to navigate technical challenges like integrating with existing systems, determining which components needed replacement and choosing materials that would endure harsh agricultural environments.
To ensure the design’s success, they collaborated closely with the client to identify key requirements, including forward and reverse compatibility, service conditions and projected production volumes. Factors like the longevity of materials, corrosion resistance and ease of serviceability were considered essential in the design process, especially given the tough conditions Big Bud tractors often operate in. The team had to make decisions on component types, from plastic versus metal connectors to the environmental impact of materials.
Ultimately, they created a solution that not only solved the immediate issue of finding replacement parts but also improved the functionality of the tractors. This process included considering future maintenance and ease of service, making the new system both user-friendly and robust enough to extend the tractor’s operational life significantly. The successful development led to offering retrofit kits to other Big Bud tractor owners, ensuring that these machines could continue to operate reliably in agricultural environments.
“We’ll let the requirements drive the process,” technical sales director Lorne Grieger says. “It is understanding what the requirements are for the equipment and the conditions that it’ll be operated in once it leaves our facility.” So they take the time to work with the client to understand all those details up front.
“And sometimes the clients don’t really know what they want either,” Schultz adds. “So they’re relying on our guidance and experience to steer them in the right direction with the product design.”
Print this page
Advertisement
<