
Choosing an Image Sensor for Machine Vision
By Mark Butler
Automation Motion Control Machine Building machine visionPicking the right image sensor for a machine vision application requires tradeoffs.
The camera is the eye of a machine vision system, but the heart of a camera is the image sensor. Sensor choice dictates the accuracy, throughput, sensitivity and cost of a machine vision system and must be made with full understanding of the application’s needs. A basic understanding of key sensor attributes will allow developers to quickly narrow their search for the right sensor.
Most machine vision users recognize that the camera is a key system element and often refer to it as the vision system’s “sensor.” But the camera is itself a complex system, including lenses, signal processing, communications interfaces and, at the core, the device that converts photons to electrons: the true image sensor. While the lens and other elements work to support the camera’s capability, the sensor ultimately sets the camera’s maximum performance limits.
Much discussion within the industry has centered on the question of fabrication technology, debating the relative merits of CMOS and CCD sensors. Both technologies offer advantages and drawbacks, and sensors made from them will have differing attributes. What the user cares about, however, is not the “how” of a sensor, but its performance in the final application. Application needs, not technology, drive sensor choice.
Three sensor characteristics are of critical interest when making a selection for a given application: dynamic range, speed and responsivity. Dynamic range determines the quality of the image, or the ability of a system to determine critical information from minute subtleties within the image. Sensor speed measures how many images per second the sensor can produce and sets the throughput that the system can achieve.
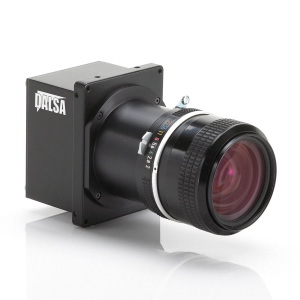
Responsivity measures the sensor’s efficiency in converting photons to electrons and determines the illumination levels and time a system needs to capture a usable image. Sensor technology and design both create interactions among these characteristics, so system developers must make trade-offs when choosing a sensor. Exploring these characteristics in detail can assist in making those trade-offs.
Sensor Trade-offs
The dynamic range characteristic of a sensor may be its most confusing. Because most machine vision systems are digital, dynamic range is influenced by two components, the analog circuitry of the sensor and the digital circuitry, which may not be part of the sensor. The analog component represents the range of exposures (illumination x time) over which the sensor can operate.